Korozja to proces, w którym żelazo jest degradowane przez obecność różnych czynników utleniających w środowisku. Korozja przybiera różne formy i może mieć wiele przyczyn. Jednym z typowych przykładów jest proces rdzewienia, w którym żelazo utlenia się w obecności wilgoci. Korozja to poważny problem dla producentów budynków, łodzi, samolotów, samochodów i innych wyrobów metalowych. Na przykład, gdy żelazo jest używane jako część mostu, integralność strukturalna żelaza, która może zostać uszkodzona przez korozję, ma kluczowe znaczenie dla bezpieczeństwa osób korzystających z mostu. Zobacz krok 1 poniżej, aby zacząć uczyć się, jak chronić żelazo przed zagrożeniem korozją i jak spowolnić tempo korozji.
Krok
Metoda 1 z 3: Zrozumienie powszechnych rodzajów korozji żelaza
Ponieważ obecnie stosuje się tak wiele różnych rodzajów żelaza, budowniczowie i producenci muszą chronić przed wieloma rodzajami korozji. Każde żelazo ma unikalne właściwości elektrochemiczne, które określają, na jaki rodzaj korozji (jeśli w ogóle) jest podatne. Poniższa tabela opisuje niektóre popularne żelazka i rodzaje korozji, którym mogą podlegać.
Żelazo | Podatność na korozję żelaza | Ogólne techniki zapobiegania | Aktywność galwaniczna* |
---|---|---|---|
Stal nierdzewna (pasywna) | Jednolity atak, galwaniczny, perforowany, spękany (wszystkie głównie w wodzie morskiej) | Czyszczenie, powłoka ochronna lub uszczelnienie | Niski (początkowe formy korozji tworzą ochronną warstwę oksydacyjną) |
Żelazo | Jednolity atak, galwaniczny, pęknięcie | Czyszczenie, powłoka ochronna lub uszczelnienie, galwanizacja, antykorozyjne | Wysoka |
Mosiądz | Jednolity atak, odcynkowanie, stres | Czyszczenie, powłoka ochronna lub uszczelnienie (zwykle olej lub lakier), dodawanie ołowiu, aluminium lub arsenu do stopów | Obecnie |
Aluminium | Galwaniczne, dziury, pęknięcia | Czyszczenie, powłoka ochronna lub uszczelnienie, anoda, galwanizacja, ochrona katodowa, izolacja elektryczna | Wysoka (początkowa korozja tworzy odporną warstwę utleniania) |
Miedź | Galwaniczna, dziurawa, estetyczna plama | Czyszczenie, nakładanie powłok ochronnych lub uszczelnianie, dodawanie niklu do stopów metali (szczególnie do solanki) | Niska (początkowa korozja tworzy oporową patynę) |
*Należy pamiętać, że kolumna „Aktywność galwaniczna” odnosi się do powiązanej aktywności chemicznej żelaza opisanej w tabeli galwanicznej źródła odniesienia. Na potrzeby tej tabeli „im wyższa aktywność galwaniczna żelaza, tym szybciej ulegnie korozji galwanicznej w połączeniu z mniej aktywnym żelazem”.
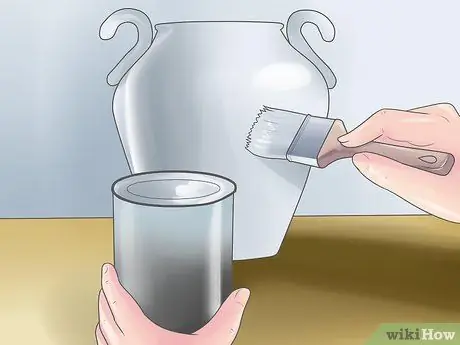
Krok 1. Zapobiegaj równomiernej korozji ataku, chroniąc powierzchnię żelaza
Korozja jednorodna (czasami skracana do korozji „jednorodnej”) jest rodzajem korozji, która występuje w związku z tym w sposób jednolity na odsłoniętych powierzchniach metalowych. W przypadku tego typu korozji cała powierzchnia żelaza jest atakowana przez korozję, a zatem korozja postępuje w równomiernym tempie. Na przykład, jeśli niezabezpieczony metalowy dach jest regularnie wystawiony na deszcz, cała powierzchnia dachu będzie miała kontakt z taką samą ilością wody, a tym samym będzie korodować w równomiernym tempie. Najłatwiejszym sposobem ochrony przed jednolitym atakiem jest zwykle umieszczenie bariery ochronnej między jagodą a środkiem żrącym. Może to być wiele rzeczy - farba, uszczelki olejowe, „lub” rozwiązanie elektrochemiczne, takie jak galwaniczna powłoka cynkowa.
W sytuacjach podziemnych lub zanurzeniowych osłona katodowa jest również dobrym rozwiązaniem
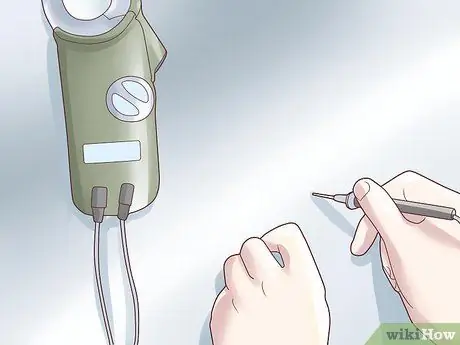
Krok 2. Zapobiegaj korozji galwanicznej, odcinając przepływ jonów z jednego żelaza do drugiego
Jedną z ważnych form korozji, która może wystąpić niezależnie od wytrzymałości fizycznej żelaza, jest korozja galwaniczna. Korozja galwaniczna występuje, gdy dwa żelazka o różnych potencjałach elektrod wchodzą w kontakt z obecnością elektrolitu (takiego jak słona woda), który tworzy ścieżkę przewodnictwa elektrycznego między nimi. Kiedy tak się dzieje, jony żelaza przepływają z bardziej aktywnego żelaza do mniej aktywnego żelaza, powodując, że bardziej aktywne żelazo koroduje szybciej, a mniej aktywne żelazo koroduje wolniej. W praktyce oznacza to, że korozja rozwinie się na bardziej aktywnym żelazie w miejscu styku dwóch żelazek.
- Każda metoda ochrony, która zapobiega przepływowi jonów między żelazkami, może zatrzymać korozję galwaniczną. Nadanie żelazu warstwy ochronnej może zapobiec tworzeniu się elektrolitów z otoczenia w tworzeniu ścieżki przewodzenia elektrycznego między dwoma żelazkami, które również dobrze sprawdzają się w elektrochemicznych procesach ekranowania, takich jak galwanizacja i anoda. Można również zapobiegać korozji galwanicznej stykających się powierzchni izolujących elektrycznie.
- Ponadto zastosowanie ochrony katodowej lub anodowej może chronić ważne żelazo przed korozją galwaniczną. Więcej informacji znajdziesz poniżej.
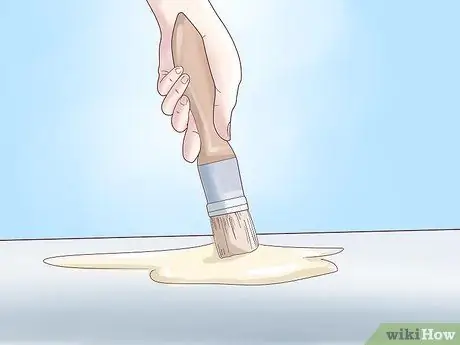
Krok 3. Zapobiegaj korozji wżerowej, chroniąc powierzchnię żelaza, unikając źródeł chlorków w środowisku oraz unikając nacięć i zadrapań
Wżery to forma korozji, która zachodzi na skalę mikroskopową, ale może mieć poważne konsekwencje. Otwory są głównym problemem w przypadku żelaza, które swoją odporność na korozję zawdzięcza cienkiej warstwie związku pasywnego na swojej powierzchni, ponieważ ta forma korozji może prowadzić do uszkodzeń strukturalnych w sytuacjach, w których powłoka ochronna normalnie temu zapobiega. Dziury powstają tam, gdzie mały kawałek żelaza traci swoją pasywną warstwę ochronną. Kiedy tak się dzieje, korozja galwaniczna zachodzi w mikroskopijnej skali, prowadząc do powstawania maleńkich otworów w żelazie. W tej dziurze środowisko staje się zakwaszone, co przyspiesza proces. Otworom zwykle zapobiega się przez nałożenie warstwy ochronnej na powierzchnię metalu i/lub zastosowanie ochrony katodowej.
Wystawienie na działanie środowiska o wysokiej zawartości chlorków (takich jak na przykład słona woda) może przyspieszyć proces perforacji
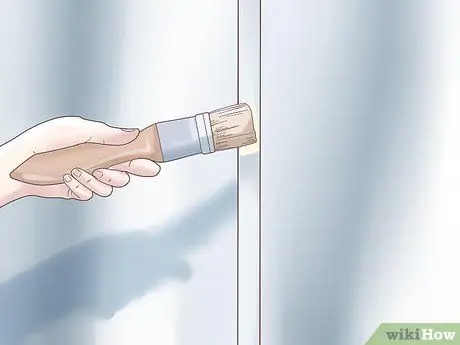
Krok 4. Zapobiegaj pękaniu korozyjnemu, minimalizując ciasne przestrzenie w projekcie obiektu
Korozja pękająca występuje w przestrzeniach metalowych obiektów, gdzie dostęp do otaczającego płynu (powietrza lub cieczy) jest bardzo słaby - na przykład pod śrubami, pod podkładkami, pod pąkle lub między połączeniami zawiasowymi. Korozja pękająca występuje, gdy szczelina między metalowymi powierzchniami jest wystarczająco szeroka, aby umożliwić wniknięcie cieczy, ale na tyle wąska, że ciecz jest trudna do wydostania się i staje w miejscu. Środowisko w tej niewielkiej przestrzeni staje się korozyjne, a żelazo zaczyna korodować w procesie podobnym do korozji pękania. Zapobieganie pękaniu korozyjnemu jest generalnie problemem projektowym. Minimalizując występowanie wąskich szczelin w konstrukcji obiektów metalowych poprzez zakrycie tych szczelin lub zapewnienie cyrkulacji, możliwe jest zminimalizowanie korozji pęknięć.
Korozja pękająca jest szczególnym problemem podczas pracy z żelazem, takim jak aluminium, które ma pasywną zewnętrzną warstwę ochronną, ponieważ mechanizmy korozji pęknięć mogą przyczyniać się do rozpadu tej powłoki
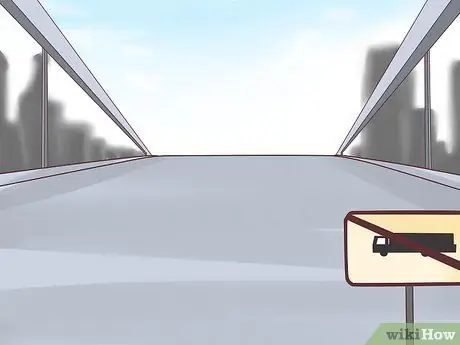
Krok 5. Zapobiegaj korozji naprężeniowej, stosując tylko bezpieczne obciążenia i/lub wyżarzając
Pękanie korozyjne naprężeniowe (SCC) jest formą związanego z korozją uszkodzenia konstrukcji, która jest problemem dla inżynierów projektujących konstrukcje budowlane, które przenoszą krytyczne obciążenia. Wraz z pojawieniem się SCC żelazo podtrzymujące obciążenie tworzy pęknięcia i pęknięcia poniżej swojej granicy obciążenia - w ciężkich przypadkach w mniejszym stopniu. W obecności jonów korozyjnych, mikroskopijne drobne pęknięcia w żelazie spowodowane naprężeniem rozciągającym ciężkich ładunków rozprzestrzeniają się, gdy jony korozyjne docierają do wierzchołka pęknięcia. Powoduje to powolne powiększanie pęknięcia i może prowadzić do uszkodzenia konstrukcji. SCC jest szczególnie niebezpieczny, ponieważ może wystąpić nawet w obecności materiałów, które ogólnie są mniej korozyjne dla żelaza. Oznacza to, że ta szkodliwa korozja występuje, podczas gdy reszta powierzchni żelaza wydaje się nienaruszona.
- Zapobieganie SCC jest częściowo problemem projektowym. Na przykład wybór materiałów odpornych na SCC w środowisku, w którym żelazko będzie działać, i zapewnienie, że materiał żelazny zostanie odpowiednio przetestowany pod kątem obciążenia, może pomóc w zapobieganiu SCC. Ponadto proces wzmacniania żelaza może usunąć naprężenia szczątkowe z projektu.
- Wiadomo, że SCC nasila się pod wpływem wysokich temperatur i obecności rozpuszczonych płynów zawierających chlorki.
Metoda 2 z 3: Zapobieganie korozji za pomocą rozwiązań domowych
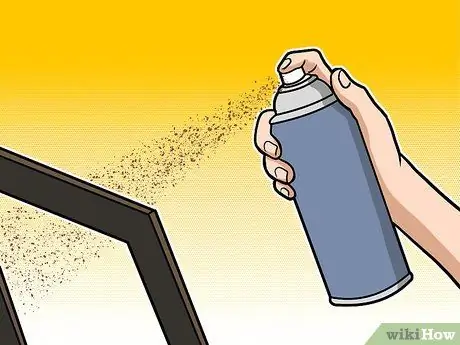
Krok 1. Pomaluj żelazną powierzchnię
Prawdopodobnie najczęstszą i najtańszą metodą ochrony żelaza przed korozją jest po prostu pokrycie go warstwą farby. Proces korozji obejmuje oddziaływanie wilgoci i utleniaczy z powierzchnią żelaza. W ten sposób, jeśli żelazo jest pokryte ochronną barierą malarską, ani wilgoć, ani środki utleniające nie mogą wejść w kontakt z samym żelazkiem i nie występuje korozja.
- Jednak sama farba jest podatna na degradację. Maluj, gdy coś jest wyszczerbione, zużyte lub uszkodzone. Jeśli farba degraduje się tak, że żelazko jest odsłonięte, należy sprawdzić pod kątem korozji lub uszkodzenia odsłoniętego żelazka.
-
Istnieje wiele metod malowania powierzchni metalowych. Ślusarze często stosują kilka z tych metod, aby zapewnić dokładną powłokę wszystkich metalowych przedmiotów. Poniżej kilka przykładowych metod z komentarzami na temat ich użycia:
- Pędzel - używany do trudno dostępnych miejsc.
- Wałek - służy do przykrywania dużych przestrzeni. Tanio i łatwo.
- Natrysk powietrzny - stosowany do pokrywania dużych przestrzeni. Szybszy, ale nie tak łatwy jak wałek (marnotrawstwo farby).
- Natrysk bezpowietrzny/Natrysk bezpowietrzny elektrostatyczny - stosowany do pokrywania dużych przestrzeni. Szybki i umożliwia różne stopnie gęstej/rzadkiej konsystencji. Nie tak marnotrawna jak zwykła woda w sprayu. Sprzęt jest dość drogi.

Krok 2. Użyj farby morskiej do żelaza wystawionego na działanie wody
Przedmioty metalowe, które mają regularny (lub stały) kontakt z wodą, takie jak łodzie, wymagają specjalnej farby chroniącej przed wysokim prawdopodobieństwem korozji. W tej sytuacji „normalna” korozja w postaci rdzewienia nie jest jedynym problemem (choć jest ona dość duża), ponieważ życie morskie (pąkle itp.) może rozwijać się na niezabezpieczonym żelazie, które może być źródłem zużycia i łez. dodatkowa korozja. Aby chronić metalowe przedmioty, takie jak łodzie i inne, należy użyć wysokiej jakości epoksydowej farby morskiej. Ten rodzaj farby nie tylko chroni żelazo przed wilgocią, ale także zapobiega rozwojowi życia morskiego na jego powierzchni.
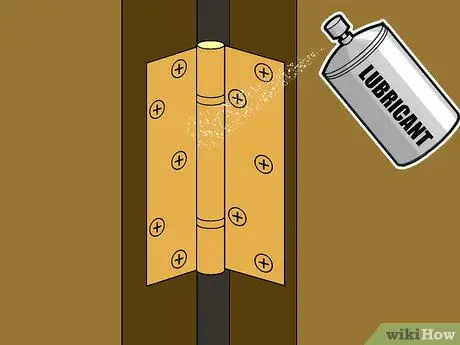
Krok 3. Nałóż smar ochronny na ruchome części metalowe
W przypadku płaskich i statycznych powierzchni metalowych farba doskonale sprawdza się w utrzymywaniu wilgoci i zapobieganiu korozji bez wpływu na użyteczność żelazka. Jednak farba zwykle nie nadaje się do ruchomych części metalowych. Na przykład, jeśli malujesz na zawiasie drzwi, gdy farba wyschnie, utrzyma zawias, blokując jego ruch. Jeśli otworzysz drzwi siłą, farba pęknie, pozostawiając miejsce na dotarcie wilgoci do żelazka. Lepszym wyborem dla części żelaznych, takich jak zawiasy, przeguby, wały itp., jest odpowiednie smarowanie nierozpuszczalne w wodzie. Ta dokładna warstwa lubrykantu odpycha wilgoć, zapewniając jednocześnie płynny i łatwy ruch metalowych części.
Ponieważ smary nie wysychają w miejscu jak farba, mogą z czasem ulegać degradacji i wymagają regularnego ponownego użycia. Okresowo ponownie nakładaj smar na części metalowe, aby zapewnić ich skuteczność jako uszczelnienie ochronne
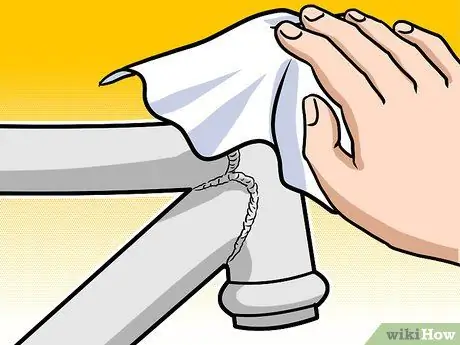
Krok 4. Dokładnie oczyść metalową powierzchnię przed malowaniem lub smarowaniem
Niezależnie od tego, czy używasz zwykłej farby, farby morskiej, czy ochronnego smarowania/uszczelniania, powinieneś upewnić się, że żelazko jest czyste i suche przed rozpoczęciem procesu aplikacji. Upewnij się, że żelazko jest wolne od wszelkich istniejących zabrudzeń, smarów, pozostałości po spawaniu lub korozji, ponieważ może to zmarnować wysiłek, przyczyniając się do korozji w przyszłości.
- Gleba, olej i inne zanieczyszczenia mogą zakłócać działanie farby i smaru, zapobiegając przyleganiu farby lub smaru bezpośrednio do powierzchni metalu. Na przykład, jeśli malujesz na blasze stalowej ze skrawkiem żelaza na wierzchu, farba wyschnie na wierzchu mielenia, pozostawiając pustą przestrzeń w żelazku pod spodem. Czy i kiedy ostrzałka spada. Odsłonięta część będzie podatna na korozję.
- Jeśli malujesz lub smarujesz żelazną powierzchnię z istniejącą już korozją, Twoim celem powinno być sprawienie, aby powierzchnia była jak najbardziej gładka i normalna, aby zapewnić najlepszą możliwą przyczepność uszczelnienia do żelazka. Użyj szczotki drucianej, papieru ściernego i/lub chemicznego odrdzewiacza, aby usunąć jak najwięcej korozji.
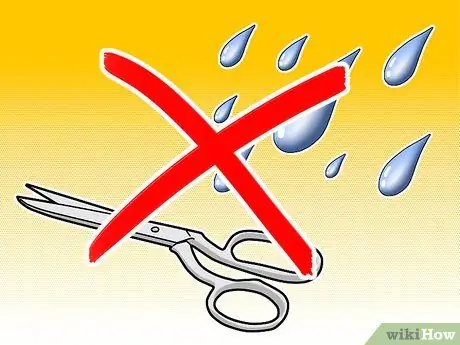
Krok 5. Trzymaj niezabezpieczone produkty żelazne z dala od wilgoci
Jak wspomniano powyżej, większość form korozji nasila wilgoć. Jeśli nie możesz nałożyć ochronnej warstwy farby lub uszczelnienia na żelazko, upewnij się, że nie jest ono wystawione na działanie wilgoci. Dążenie do utrzymania w stanie suchym niezabezpieczonych narzędzi żelaznych może zwiększyć ich użyteczność i przedłużyć ich żywotność. Jeśli żelazko jest narażone na działanie wody lub wilgoci, należy je wyczyścić i wysuszyć natychmiast po użyciu, aby zapobiec korozji.
Oprócz monitorowania narażenia na wilgoć podczas użytkowania, metalowe przedmioty należy przechowywać w pomieszczeniu, w czystym i suchym miejscu. W przypadku dużych przedmiotów, które nie mieszczą się w szafce lub szafce, przykryj przedmiot szmatką. Pomaga to odpychać wilgoć z powietrza i zapobiega gromadzeniu się kurzu na powierzchni
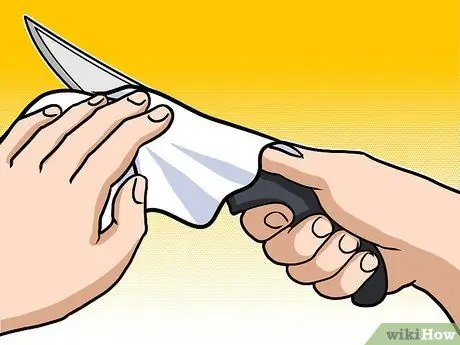
Krok 6. Upewnij się, że metalowa powierzchnia jest tak czysta, jak to możliwe
Po każdym użyciu metalowego przedmiotu, niezależnie od tego, czy metal jest pomalowany czy nie, należy wyczyścić jego powierzchnię użytkową, usuwając wszelkie zabrudzenia, tłuszcz i kurz. Nagromadzenie brudu na powierzchni metalu może przyczyniać się do zużycia żelazka i/lub jego powłoki ochronnej, prowadząc z czasem do korozji.
Metoda 3 z 3: Zapobieganie korozji za pomocą zaawansowanych rozwiązań elektrochemicznych

Krok 1. Zastosuj proces galwanizacji
Żelazo ocynkowane to żelazo, które zostało pokryte cienką warstwą cynku w celu ochrony przed korozją. Cynk jest bardziej aktywny chemicznie niż znajdujące się pod nim żelazo, więc utlenia się pod wpływem powietrza. Gdy warstwa cynku ulegnie utlenieniu, tworzy warstwę ochronną, zapobiegając dalszej korozji znajdującego się pod nią żelaza. Najpopularniejszym obecnie rodzajem galwanizacji jest proces zwany cynkowaniem ogniowym, w którym kawałek żelaza (zwykle stali) jest zanurzany w gorącym stopionym cynku w celu uzyskania jednolitej powłoki.
-
Proces ten obejmuje obchodzenie się z chemikaliami przemysłowymi, z których niektóre są niebezpieczne w temperaturze pokojowej, w bardzo wysokich temperaturach i nie powinny być podejmowane przez nikogo poza przeszkolonym profesjonalistą. Poniżej przedstawiamy podstawowe etapy procesu cynkowania ogniowego stali:
- Stal jest czyszczona gorącym roztworem w celu usunięcia brudu, oleju, farby itp., a następnie dokładnie spłukiwana.
- Stal zanurza się w kwasie w celu usunięcia zgorzeliny walcowniczej, a następnie płucze.
- Materiał zwany „topnikiem” nakłada się na stal i pozostawia do wyschnięcia. Pomaga to końcowej warstwie cynku przykleić się do stali.
- Stal zanurza się w gorącym cynku i pozostawia do osiągnięcia temperatury cynku.
- Stal jest chłodzona w „zbiorniku chłodzącym” wypełnionym wodą.
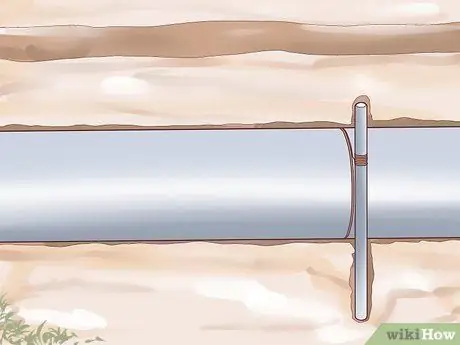
Krok 2. Użyj anody protektorowej
Jednym ze sposobów ochrony żelaznych obiektów przed korozją jest elektryczne przymocowanie do niego małego, reaktywnego metalu zwanego „anodą ofiarną”. Ze względu na elektrochemiczny związek między większym żelazem a małym reaktywnym ciałem (który jest krótko opisany poniżej), tylko małe i reaktywne żelazo ulegnie korozji, pozostawiając duże i ważne żelazo nienaruszone. Gdy anoda protektorowa koroduje całkowicie, należy ją wymienić, w przeciwnym razie większe żelazo ulegnie korozji. Ta metoda ochrony przed korozją jest zwykle stosowana w przypadku konstrukcji podziemnych, takich jak podziemne zbiorniki magazynowe, lub obiektów, które mają stały kontakt z wodą, takich jak łodzie.
- Anoda protektorowa wykonana jest z kilku różnych rodzajów reaktywnego żelaza. Cynk, aluminium i magnez to trzy najczęściej używane w tym celu żelazka. Ze względu na właściwości chemiczne tych materiałów, cynk i aluminium są powszechnie stosowane do materiałów żelaznych w wodzie słonej, podczas gdy magnez jest bardziej odpowiedni do celów w wodzie słodkiej.
- Anody protektorowe mogą być stosowane ze względu na sam proces chemiczny korozji. Gdy żelazny obiekt koroduje, w naturalny sposób tworzą się obszary chemicznie podobne do anody i katody w ogniwie elektrochemicznym. Elektrony przepływają z anody na powierzchni żelaza do otaczającego elektrolitu. Ponieważ anoda protektorowa jest bardzo reaktywna w porównaniu z chronionym żelazem, sam obiekt staje się w porównaniu z tym wysoce katodowy, a zatem elektrony wypływają z anody protektorowej, powodując korozję, ale nie resztę żelaza.
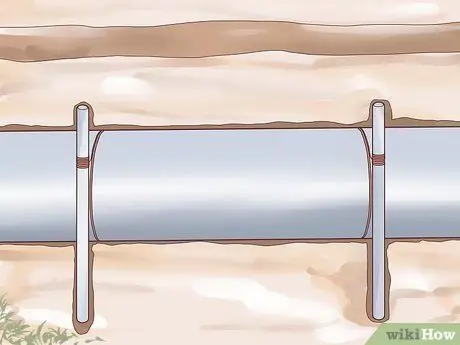
Krok 3. Użyj „prądu pod wrażeniem”
Ponieważ proces elektrochemiczny stojący za korozją żelaza obejmuje przepływ prądu elektrycznego w postaci elektronów wypływających z żelaza, możliwe jest użycie zewnętrznego źródła prądu elektrycznego do kontrolowania przepływu korozyjnego i zapobiegania korozji. Ten proces (zwany „prądem pod wrażeniem”) polega na ciągłym ujemnym ładunku żelaza na chronionym żelazie. Ładunek ten przytłacza przepływ, powodując wypływ elektronów z żelaza, zapobiegając korozji. Ten rodzaj ochrony jest zwykle stosowany w przypadku podziemnych konstrukcji żelaznych, takich jak zbiorniki magazynowe i rury.
- Należy pamiętać, że rodzaj prądu elektrycznego stosowanego w systemach ochrony pod wrażeniem prądu to zwykle prąd stały (DC).
- Zazwyczaj pod wrażeniem prądu, który zapobiega korozji, jest generowany przez zakopanie dwóch żelaznych anod w ziemi w pobliżu chronionego metalowego przedmiotu. Prąd elektryczny jest przesyłany przez drut izolacyjny przy anodzie, który następnie przepływa przez ziemię do metalowego przedmiotu. Energia elektryczna przepływa przez żelazne przedmioty, a następnie wraca do źródła energii elektrycznej (generatory, prostowniki itp.) przez przewody izolacyjne.
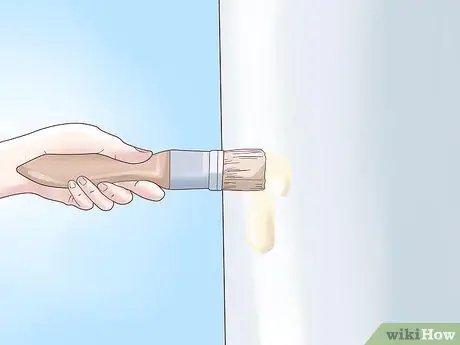
Krok 4. Użyj anodowania
Anodowanie to specjalna warstwa ochronna powierzchni stosowana do ochrony żelaza przed korozją. Jeśli kiedykolwiek widziałeś jasny żelazny karabińczyk, widziałeś kolorową anodowaną żelazną powierzchnię. Zamiast fizycznego nakładania powłoki ochronnej, takiej jak farba, anodowanie wykorzystuje prąd elektryczny do nałożenia na żelazo warstwy ochronnej, która zapobiega prawie wszystkim formom korozji.
- Proces chemiczny związany z anodowaniem polega na tym, że wiele żelazek, takich jak aluminium, naturalnie tworzy produkty chemiczne zwane tlenkami w kontakcie z tlenem znajdującym się w powietrzu. Powoduje to, że żelazo zwykle ma cienką zewnętrzną warstwę tlenku, która chroni (w różnym stopniu, w zależności od żelaza) przed dalszą korozją. Prąd elektryczny używany w procesie anodowania zwykle tworzy grubszą warstwę tego tlenku na powierzchni żelaza niż zwykle, zapewniając doskonałą ochronę przed korozją.
-
Istnieje kilka różnych sposobów przekazywania żelaza. Poniżej znajdują się podstawowe kroki jednego z procesów anodowania. Zobacz Jak anodować aluminium, aby uzyskać więcej informacji.
- Aluminium jest czyszczone i odtłuszczane.
- Zanieczyszczenia z powierzchni aluminium usuwa się roztworem de-smut.
- Aluminium jest umieszczane w kąpieli kwasowej o stałym natężeniu prądu i temperaturze (na przykład 12 amperów/stopę kwadratową i 70-72 stopnie F (21-22 stopnie C).
- Aluminium jest usuwane i płukane.
- Glin jest opcjonalnie wprowadzany do barwnika w temperaturze 100-140 stopni F (38-60 stopni C).
- Aluminium uszczelnia się poprzez zanurzenie go we wrzącej wodzie na 20-30 minut.
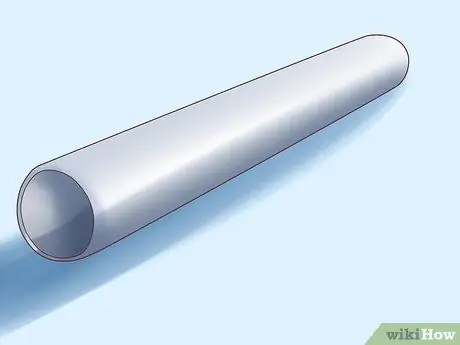
Krok 5. Użyj pasywnego żelaza
Jak wspomniano powyżej, niektóre żelazo naturalnie tworzy ochronną warstwę tlenku po wystawieniu na działanie powietrza. Niektóre żelazo tworzy tę warstwę tlenku tak skutecznie, że staje się chemicznie nieaktywna. Mówimy, że żelazo jest „pasywne” w odniesieniu do „pasywnego” procesu, w którym staje się mniej reaktywne. W zależności od zastosowania, pasywne przedmioty żelazne mogą nie „potrzebować” dodatkowej ochrony, aby były odporne na korozję.
-
Jednym z dobrze znanych przykładów żelaza pasywnego jest stal nierdzewna. Stal nierdzewna jest powszechnym stopem stali i chromu, który jest odporny na korozję w większości warunków bez konieczności ochrony. W przypadku większości codziennych zastosowań korozja zwykle nie dotyczy stali nierdzewnej.
Trzeba jednak powiedzieć, że w pewnych warunkach stal nierdzewna nie jest w 100% odporna na korozję - na przykład w słonej wodzie. Podobnie wiele żelazek pasywnych staje się niepasywnych w ekstremalnych warunkach pogodowych i dlatego nie nadaje się do wszystkich zastosowań
Porady
- Uważaj na korozję międzykrystaliczną. Wpływa to na zdolność żelazka do formowania lub manipulowania i zmniejsza ogólną wytrzymałość żelazka.
- American Boat and Yacht Council generalnie zaleca wiązanie łodzi. Jednak łodzie aluminiowe i stalowe nie powinny być przypinane taśmami, aby zapobiec korozji żelaza.
Ostrzeżenie
- Nigdy nie zostawiaj mocno skorodowanych części metalowych w pojazdach lub łodziach. Stopień korozji jest różny, ale każda korozja może wskazywać na poważne uszkodzenie konstrukcji. Dla bezpieczeństwa wymień lub usuń wszystkie ślady korozji żelaza.
- Używając anody protektorowej, nie maluj jej. Uniemożliwiłoby to przenikanie elektronów do otoczenia, pozbawiając ich siły zapobiegającej korozji.